Home
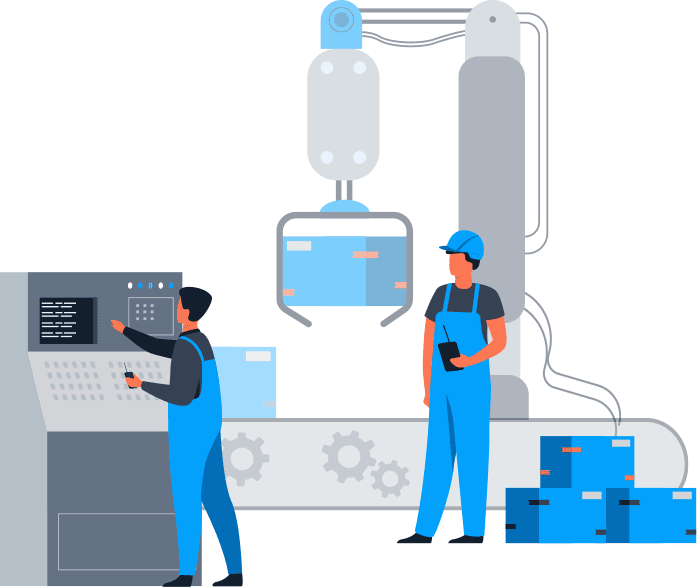
Improve operational efficiency
with our fully integrated Production & Warehouse Management System
Discover what TransLution™ could do for your business
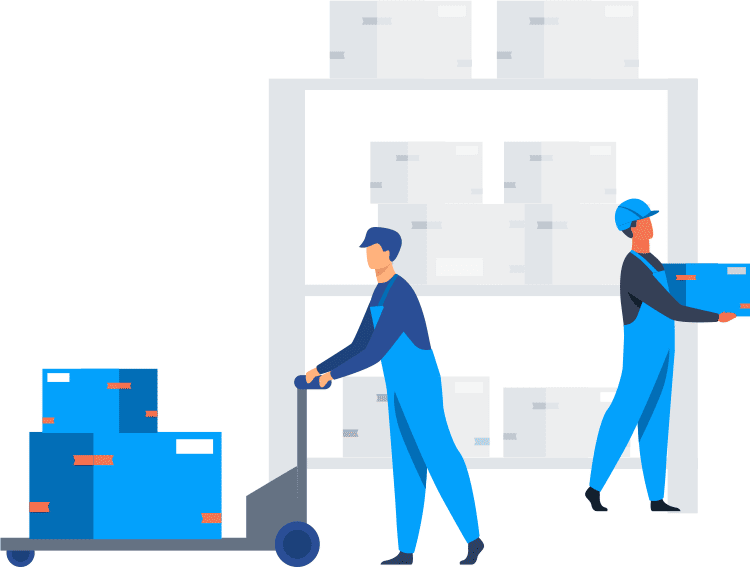
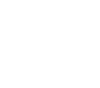
Real Time Visibility
Accurately track materials, resources, and labor across your entire enterprise.
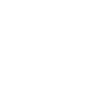
Built to Customize
Think your business is too unique to work with our software? Think again.
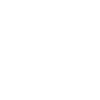
Seamless Integration
Tired of managing multiple systems? Integrate seamlessly with your ERP and other business software.
Trusted By Manufacturers Globally
- North America
- Uk & Europe
- Africa
- Australia
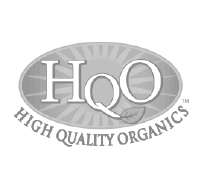
North America
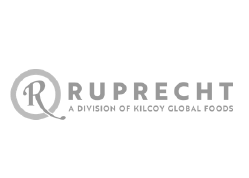
North America
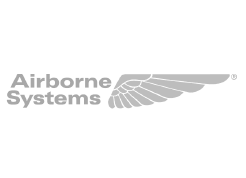
North America
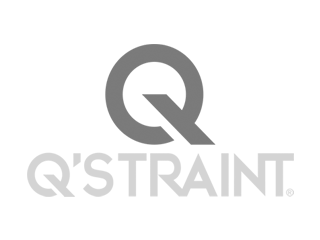
North America
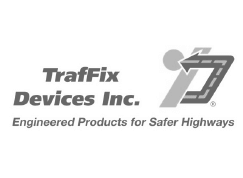
North America
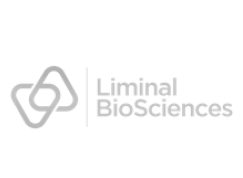
North America
Wave Goodbye
Our Customers Celebrate Freedom From these Challenges
Curious about pricing?
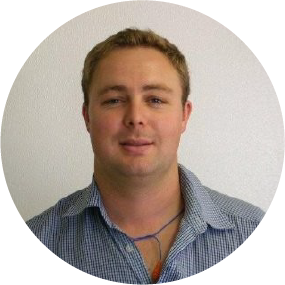
The TransLution™ System has made a huge impact on our planning. Before, it took us 3-5 days to update our plan in Excel. Now all of the stock data and figures are pulled into the spreadsheet automatically and it only takes us three hours.
Sakkie Smuts, Lancewood
Key Features
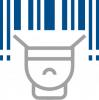
Real time data visibility
Resolve your production problems immediately with real-time access to actual data at each stage in the production process.
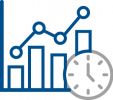
Simplicity
Train your operators and new staff to be productive in less than an hour.
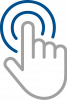
Flexibility
TransLution™ can be configured to work the way you do rather than the other way round.
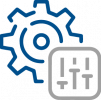
Seamless ERP Integration
Designed around an understanding of integration. Immediate and direct data collection from the shop floor
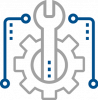
Hardware Integration
Extend your management system to integrate seamlessly with hardware and other devices.
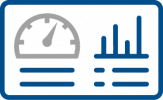
Data Visualisation
View the production data you need, when and where you need it.
Ready to see what TransLution™ Software can do for your business?
Latest News
Eya Bantu, a manufacturer of switchgear and control plant panels, has successfully implemented TransLution Software at their Port Elizabeth facility. This implementation marks the first step in their journey toward company-wide process automation and standardization.
We're excited to share several significant TransLution updates that you may have missed over recent releases. These combined enhancements dramatically improve your workflow capabilities while making the system more flexible and user-friendly than ever before.
Millennium Foods, a division of Libstar specializing in frozen ready meals, has successfully implemented TransLution Software to enhance their warehouse operations and inventory management processes. This implementation has transformed their stock control procedures from raw material receiving through to production supply.